WEAR INNOVATION – CUSTOMER STORIES
Great work worldwide
Imagine what it would do to your business to have access to the world-leading wear knowledge base. It’s not just about the world’s best material. It’s about innovation, ingenuity, and the ability to get the best out of it – every part matters. Find out what difference the support and advice from Hardox® Wearparts made to others.
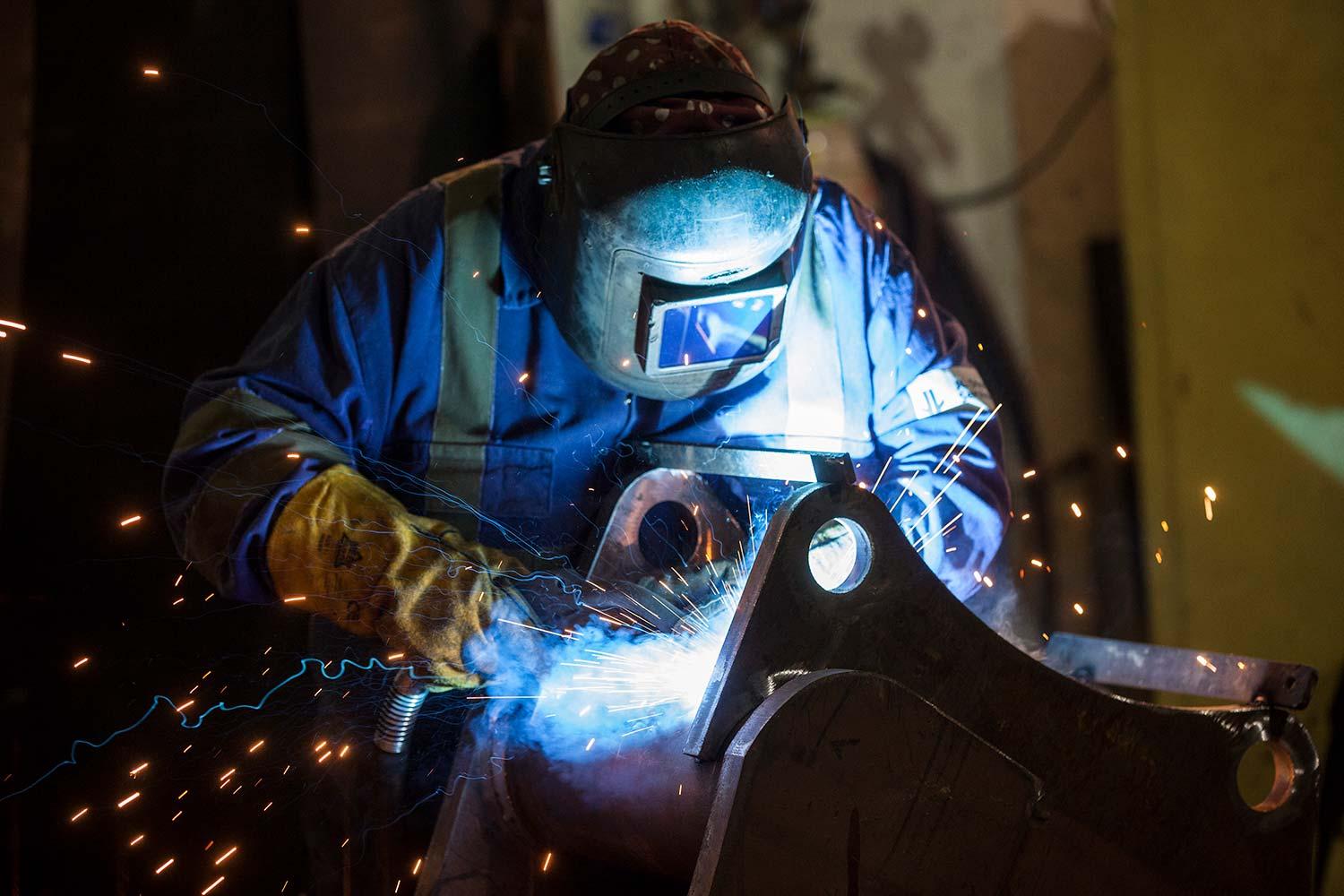
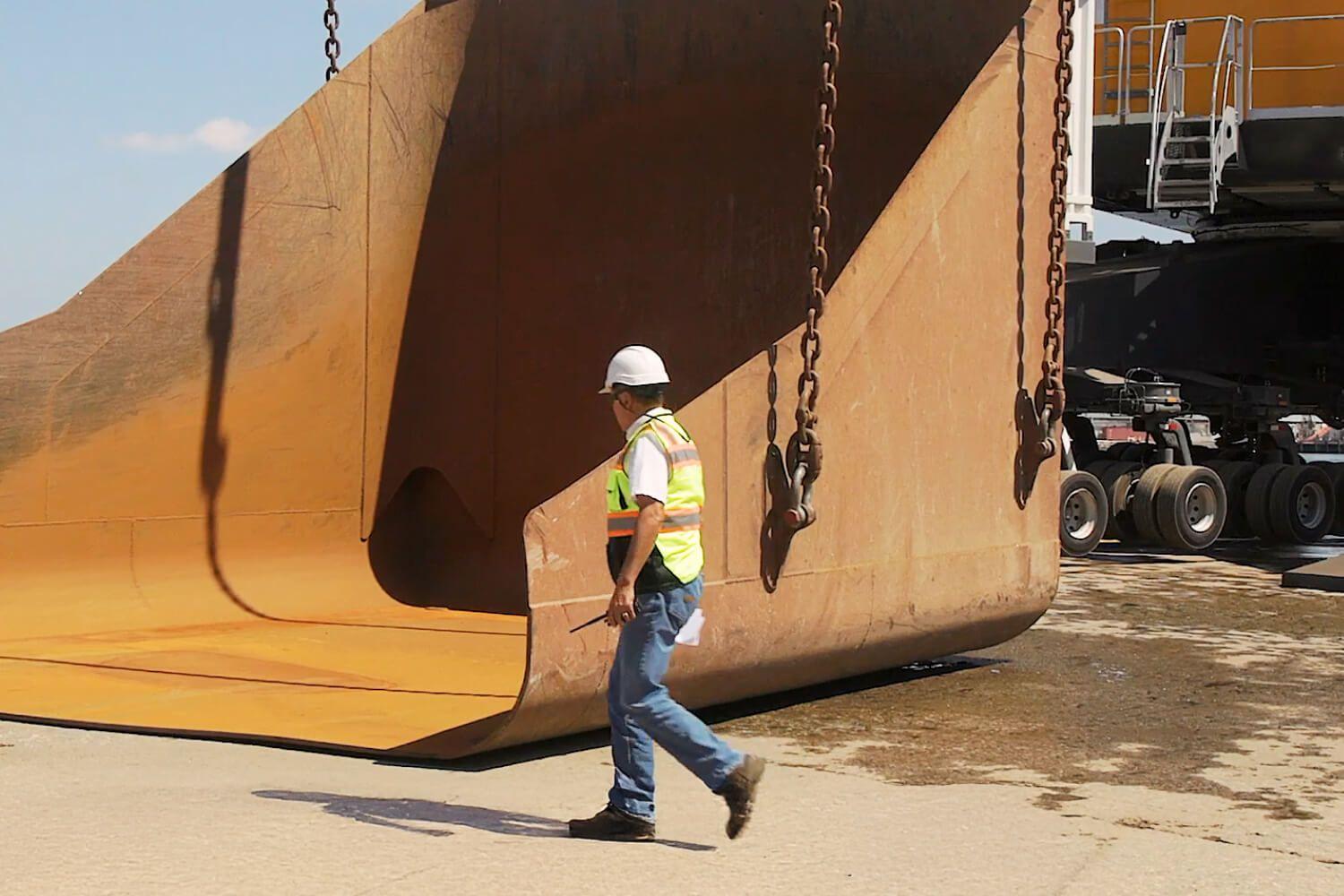
SA – CUSTOMIZED SOLUTION
Unique pan loader boosts efficiency for SA Recycling
For seafaring vessels, quick port turns and constant uptime are critical. SA Recycling moves mountains of scrap metal aboard seafaring vessels in 25% less time using a newly designed skip pan loader made from Hardox®500 Tuf.
Explore SA RecyclingREAL STEEL – CUSTOMIZED SOLUTION
Less downtime with Hardox® 600 rotor disc inserts
Learn how switching to Hardox® wear plate helped Real Steel’s customer forget all about uneven wear, time-consuming balancing, and expensive repairs.
Explore Real Steel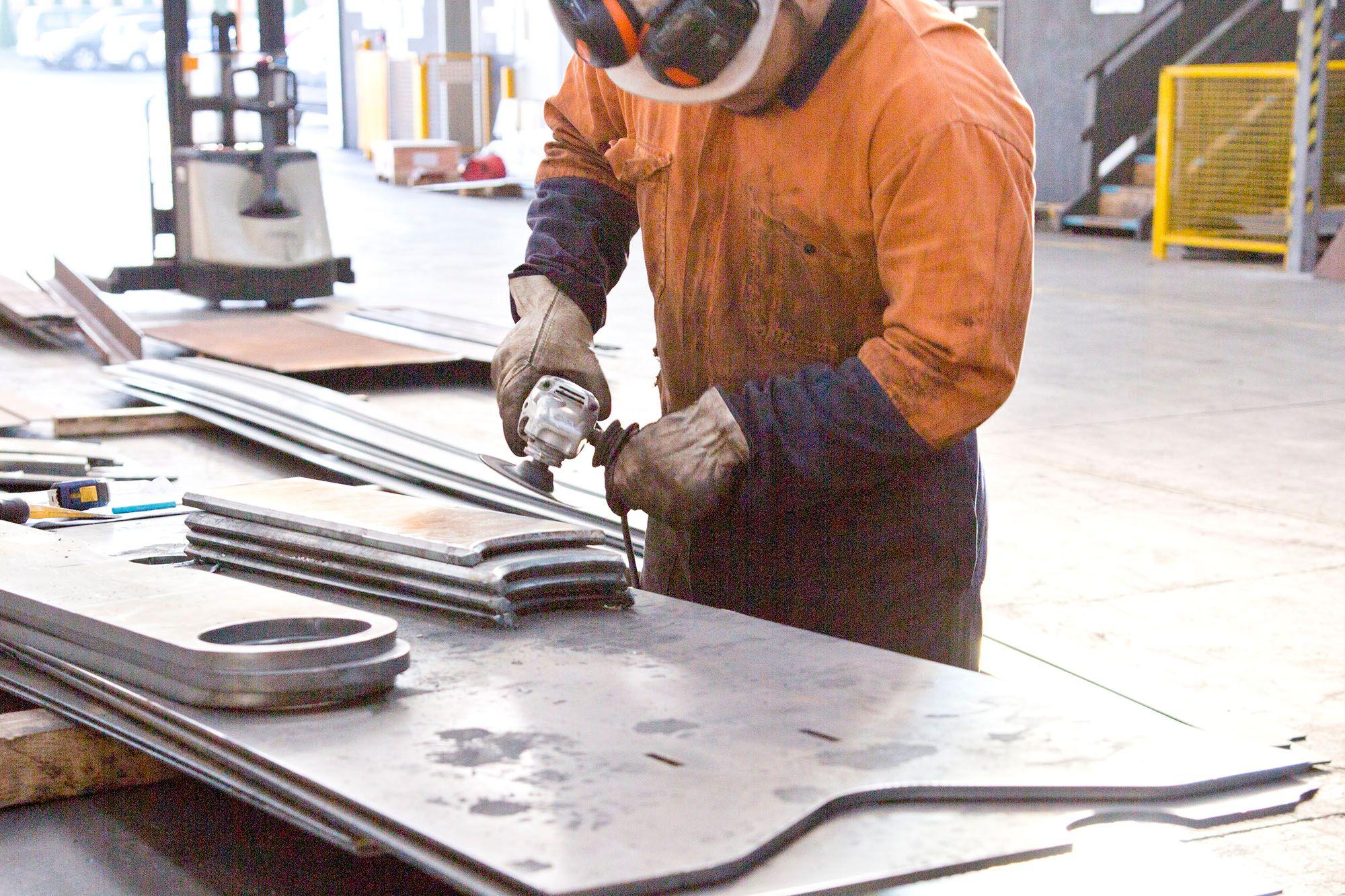
BILLERUD – CUSTOMIZED SOLUTION
Switch to Hardox® HiAce improved performance and safety
Discover how pulp and paper manufacturer Billerud cut maintenance and boosted uptime by switching from mild steel to corrosion-resistant Hardox® HiAce.
Explore Billerud